First-time Maintenance Manager
Terminology and technology have changed the role of the old hangar boss, but whether you know him as the Chief Engineer or the Person Responsible for Maintenance (PRM) much of the big picture remains the same.
I have been an AME for about 25 years now and there were several times over my career when I had learned something new from my supervisor who would then follow up with the phrase “You may need to know that for when you are a Chief Engineer one day.” Of course, that was in the days when the hangar boss was referred to as a Chief Engineer. As the regulations evolved so too did the terminology given to the person running the shop. That came to be the Director of Maintenance, the Maintenance Manager, or simply and technically the Person Responsible for Maintenance (PRM). No matter how you call it, this role will someday be attached to someone within the ranks who has developed the necessary skills and seniority to one day become next in line when the person sitting at the big desk moves on. This may be with the company you have served well over the years, or it may be filling a vacancy at another company or perhaps you will even be hired as part of a start-up business like I was at one time. Sure enough, it turned out that certain low key details were worth remembering as my innocent pondering eventually led me to my first opportunity, then another soon after that.
I started my career still green in 1987 after graduating from Centennial College in Toronto and set out to learn how to apply myself to what would become, an often challenging, yet interesting career. At that point I just wanted to get hands on and tried not to screw anything up along the way. As I settled into the routine of maintenance work and subsequently earned my AME ticket as they used to say, it became readily apparent that there would always be opportunities to learn new skills and implement new ideas.
Several years of learning about how the industry operates beyond having a growing collection of tools led me to take an active interest in company safety programs and to pursue a greater understanding of the regulations. My new familiarity with the E & I manual gave way to the Airworthiness Manual until I eventually came to a crossroads in a new Director of Maintenance position as we transitioned to the Canadian Aviation Regulations (CARs). It turned out to be a good time to be introduced to new standards for company manuals because it seemed like we all knew just enough to be confused. More specific training requirements and the introduction of human factors were also introduced as the industry itself rolled ahead into new territory with the new regs and I was determined to roll right along with it.
I had just moved a few provinces away from where I called home and started a new career for myself, and a new life for my family. Fortunately, I remembered that familiar “You may need to know…” message and made sure that I had considered much of what I had learned from my mentors over the years. Even though I did not fully comprehend the overall authority of my new position, I still learned a lot of new things in a short time.
I had stepped into a whole new learning curve working with people who were looking for answers concerning flight school operations, training needs and organizational planning. I really felt like I had something to offer from a forward thinking mindset yet also felt unworthy to carry the load of greater responsibility all at the same time. I had worked toward this kind of opportunity for some time yet there I was thinking twice about my new challenges, priorities and contributions. I nevertheless committed to the journey before me and realized that many aspects of the position were a good fit with my interests and that the rest could be learned along the way. I think it’s still like that even today.
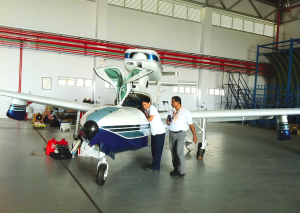
The ability of the manager to draw upon and promote the strengths of the team becomes a healthy conduit for raising self-esteem and sufficiency, all of which must not be underestimated. Adapting to the new technology is something that the manager must learn to implement in order to promote a more efficient technical resource that is both more accessible and easier to navigate for the front line technicians.
The transition from the shop floor to the maintenance office will undoubtedly inspire a new paradigm of how the work is processed and who is ultimately involved. The new PRM will come to realize an entire range of corporate duties concerning employee performance, strategic planning, goals setting and interpreting the events of the day. There is also an expected level of competence in these areas while ensuring that your department continues to perform according to some semblance of the manual.
Many managers are still getting their hands dirty in the smaller shops while others retreat to their offices where grease and tools are displaced with printer cartridges and computer applications. Either way, the Maintenance Manager must be in touch with ongoing maintenance activity on a daily basis in order to ensure that the required technical and regulatory standards continue to be met. That in itself demands frequent reflection concerning the weight of responsibility inherited with the position. Management of aircraft maintenance is not an invite to sit back with your feet up on the desk! It requires your simultaneous presence in both familiar and not so familiar corporate functions.
Transitioning to the computer age has been more difficult for some managers than it has for others. There was a time when those with the technical experience and the grey hairs of authority would be slow to catch on to the digital age but the inclusion of such technology in our everyday world has forced us all to participate on some level. It has changed the way we simply do business.
I remember working on manual revisions with a respected mentor before becoming a manager myself as we literally cut and pasted our manual revisions (yes, with scissors and tape!) into a decided format that could then be re-typed with greater speed and competence by the more efficient administrative assistant. I actually persevered through another manual editing session much in the same manner before summoning the courage to face the keyboard and the magical screen head-on for myself. I knew that it would have to happen sooner or later!
This current generation of up-and-comers grew up knowing the computer business as a normal part of growing up just like breathing. I was not interested in the new technology and my ignorance did not make it go away. For that reason, some of us found it more difficult to really catch on and become effective users. Many of the senior positions still rely on a little help from their assistants for electronic processing yet many have also become leaders themselves in the research and development of maintenance related software and applications. Those with foresight knew this to be a logical progression and have succeeded in guiding the rest of us toward a better way of doing things.
Adapting to the new technology is something that the manager must learn to implement in order to promote a more efficient technical resource that is both more accessible and easier to navigate for the front line technicians. It is no longer unusual to see a laptop loaded with aircraft manuals and tracking systems parked on a table beside the aircraft as it is being maintained. Electronic versions are easily referenced and even log book entries routinely procured using this cleaner format. It also trumps having to interpret some of those messy log entries!
Parts inventories and analytical spreadsheets represent other daily fundamentals that have been made more efficient through digital technology. Anyone entering a management position these days must prove some level of competency using computers in everyday work. Even a basic aptitude for pushing a few buttons will get you going until you are able to learn out of necessity and remain on par with the rest of the industry. I can’t help but comment on these advances without considering my own trial and error strategy that continues to be just enough to stay the course with a few memorable moments of flash and brilliant personal breakthroughs.
As a Maintenance Manager you will also attain certain skills along the way that will be necessary to the position. Troubleshooting and problem solving skills will become essential but their application is routinely tested through ongoing experience. One day there could be an elusive technical issue on an aircraft that requires additional technical support and the next day an employee is injured on the job or the parts inventory software has a glitch. All of these issues must be tended to in order for life, as we know it, to move forward. Fortunately, being surrounded by other skilled people creates team opportunities where each person contributes various skills to the daily routine.
The ability of the manager to draw upon and promote the strengths of the team becomes a healthy conduit for raising self-esteem and sufficiency, all of which must not be underestimated. Management training is an often-overlooked opportunity for the employer to further invest in some of the social and business norms known as soft skills that frequently need to be learned by new managers. We have long categorized the aircraft engineer as the strong silent type who buckles down to get the job done. We also look for certain attributes that come into play through both employee and customer relations as we are drawn more toward effective leadership.
A manager should learn to become more of a leader than a boss. Leading involves everyone and a good leader recognizes that his influence is only as solid as the group around him. In an ideal setting, everyone makes everyone else look good and we all become aware of the positive byproduct of group mentality over self-preservation. It doesn’t come easy when dealing with each other is really an ongoing lesson in patience and intuition. There is a saying that goes, “The best thing about this place is the people and the worst thing about this place is …” well, you know. This probably sounds rather extreme to some yet at the same time more believable to others, which in some way seems to qualify the origin of the statement.
A candidate for a Maintenance Manager position with an Approved Maintenance Organization (AMO) must demonstrate a confident understanding of AMO policies and quality assurance functions to Transport Canada personnel before assuming any responsibilities within the organization. CAR Standard 573.04 outlines those specific attributes and how they specifically relate to a company. The interview process is more company specific and therefore of greater value to the PRM candidate as opposed to general knowledge testing.
Chapter 573.06 goes on to describe the training requirements including those inherent to the Safety Management System (SMS). These include maintenance and flight safety philosophy, human factors, accident prevention, safety personnel responsibilities, risk management, incident/ accident reporting and investigation. I wouldn’t even have recognized these terms in relationship to my career back when I was starting out. So much of our experience has evolved since then and will continue to evolve as we embrace new ideas through involvement with manufacturing technologies and safety management just like we have seen in recent years.
The ultimate responsibility of the Maintenance Manager rests with his ability to maintain the airworthiness of the many aircraft entrusted to his care. He must dutifully represent the company and take his appointment seriously on a daily basis. He must be willing to adapt to new responsibilities and become fluent in both regulatory jargon and technical data. The Maintenance Manager must exercise control over maintenance operations and delegate signing privileges only to those who will act responsibly on his behalf.
This is only part of the picture and comes from sincerely making the most of an opportunity to jump in and learn as you go. Eventually you will be able to apply years of experience to new and appropriately sized challenges but it all takes time. At the end of the day the Maintenance Manager can also be assured that every trying experience and every learning opportunity has shaped him into becoming a valuable person to his industry.
About The Author

Stuart McAulay resides near Cambridge, Ontario and enjoys the Brantford Flying Club.
View all articles by Stuart McAulay.